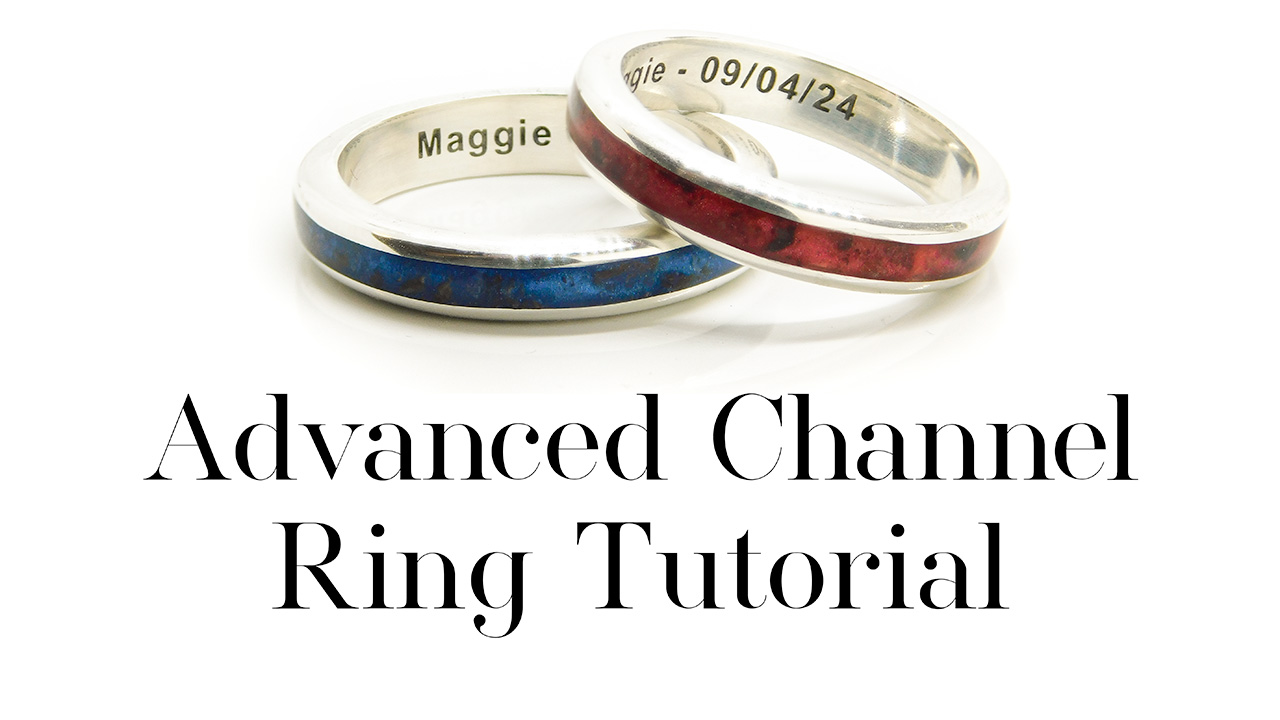
Advanced Channel Ring Tutorial – making bereavement and cremation jewellery using a direct pour technique. This technique is ideal for our channel rings here which are anti-tarnish solid silver. You don’t need a lathe for this tutorial but if you have one, definitely use it for the sanding process. You can use this technique for our partial channel rings and our channel beads too. For a channel bead we’d recommend using a rotary tool rather than a drill.
Advanced Channel Ring Tutorial Video
@keepsakersupplies Advanced Channel Ring Tutorial – making bereavement and cremation jewellery using a direct pour technique. This technique is ideal for our channel rings here which are anti-tarnish solid silver. You don’t need a lathe for this tutorial but if you have one, definitely use it for the sanding process. #memorialjewelry #uvresin #crafttutorial ♬ original sound – Keepsaker Supplies
Here’s the transcript. After your first order you’ll receive a reasonable 15%* off future purchases. We have several courses here including some free to help you learn more about making bereavement and cremation jewelry such as a cremation ring.
You’ll need the following supplies
one of our DIY ashes ring kits
the ashes/hair version of the kits contain:
- a ring setting – this is one of our full channel rings
- a practice setting for direct pour (checking colour etc)
- vinyl gloves
- resin sparkle mix (you can use eyeshadow for a custom colour!)
- a dust mask
- label backing paper
- some sandpaper
- 3 cocktail sticks
- 10g UV resin
You’ll also need your client’s cremation ashes for this Easy Opal Ashes Channel Ring Tutorial. We ask them to only send half a teaspoonful! That way, if it’s lost in the post they can send a little more.
-
- LED UV torch** or a good UV lamp for professionals
- a pestle and mortar (optional)
- Ultra Fine Sharpie
- 200g bottle of Padico Star Drop
- pre-mixed resin sparkle mix (or buy loose and mix with resin before using)
- silicone ring stick here
- a drill like this
- ultra fine foam sanding pads
- diamond polishing pastes from Amazon
Advanced Channel Ring Tutorial
Hi, I’m Nikki Lovegrove and today’s video is an advanced way to make a channel ring or bead even if you don’t have a lathe. DIY kits for these channel rings available on my website KeepsakerSupplies.com
This video may be triggering for some because I mention baby loss so please choose another video if you find this upsetting. The tutorial is dedicated to Greater Manchester Doulas CIC which is my client Amy’s organisation. They provide emotional support to mothers and families who have experienced a loss at any stage and they have funding to make this support free. They want parents to know that no matter how early the loss, they can still grieve and honour their baby in any way that feels right for them.
I’m working with dried placenta here from a baby that has passed away. I begin by cutting it into small pieces then grinding it as fine as possible. There’s a link in the description for this channel ring kit.You will also need the silicone ring holding tool and a drill, and a set of diamond polish pastes.I like to mark the sides of the ring so I know the resin is an even layer. If you’re working with multiple pieces you can write the colour on the side in Ultra Fine Sharpie, which will come off later when you polish them. Always remember to triple check your rings are the correct size. I’d recommend going a little bigger with a wider ring like this and you can send the ring to your client to try on before making it. A full channel ring can’t be resized.
The first layer should be clear resin because this helps provide a strong bond with the silver. Resin with additions such as colour or ashes isn’t as strong. I put the resin on one third of the ring, cure it for about 20 seconds under the UV lamp, then do the other two thirds the same way. Don’t forget to use a piece of cardboard covered with tin foil to protect yourself from UV damage from the lamp. If you’re using epoxy resin you’ll need a cup turner and would work in just two layers.
For the second layer I’m mixing some resin sparkle mix with a little more clear resin so it’s not too opaque to cure. Add a very thin layer of this coloured resin to one third of the ring then add some of the placenta or cremation ashes with a cocktail stick. You could also mix preserved and dried breastmilk into this layer if it’s a breastmilk ring. I’ll do a tutorial for a lock of hair channel ring soon because the hair is added after the coloured layer.
Continue with the other two thirds of the ring, overlapping the layers slightly until you have covered the base and sides of the channel with an opaque layer. I’m only curing for 20 seconds at a time because those bits will be cured fully the next time it’s under the lamp. Make sure that you wipe off any resin that goes onto the top or sides of the ring. Between each cure, you can use your fingernail to scrape off any cured bits. With this method you don’t have to worry too much about this though because you’ll be sanding the sides of the ring later and that will remove any mistakes.
Your last layers should be completely clear resin. It needs to be what’s called “proud” of the surface, so it’s domed a bit. This will be sanded down later. Work in thin layers, doing a third at a time to stop the resin pooling underneath, but again it really doesn’t matter if it pools a little bit. Check that you haven’t missed any bits and top them up with clear resin, otherwise you’ll have dips in the finished resin. Once it’s fully cured, it’s time to sand the ring. To save time you can use a coarse sanding stick or a burr bit to sand off the highest bits of resin but be careful not to sand too far down or, again, you’ll create dips. If you do that by accident, just add a bit more clear resin and cure a few times. Be super careful not to scratch the setting though!
I’m using the ultra fine sanding pads I sell on KeepsakerSupplies.com starting off with 1000 grit. Sand the sides, and the “shoulders” (or corners) of the ring, then the resin part by putting the ring on a silicone ring turning tool in a drill. Flip the ring the other way up every now and again so you don’t sand one side further down than the other. Work your way up the grits. I’m using 2000 then 3000. These will remove the scratches from the coarser grit and prepare the silver and resin for polishing.
With solid silver and gold rings, it doesn’t matter if you sand down the metal a bit but if you have a coated ring, for example something with a black rhodium plating, then this method won’t work and you should use the easy method I showed you in the opal ashes channel ring tutorial. Once you’ve done 3000 grit you can move onto the diamond polishing pastes. I’ll leave a link to them below, I got mine on Amazon. I cut a cotton rag into pieces and keep one piece with each of the pastes. Work from the smallest number grit (3000) up to the largest number (10,000) but please bare in mind that the numbers on the pastes might get smaller as you work your way up the grit. Go by the grit number rather than the paste number to be certain.
Finish off the rings with a silver polishing cloth. The inside of the ring should still be shiny but if you need to, repeat the polishing process with cotton bits in a rotary tool with the polishing paste or you can use ultra fine sanding bits if that’s easier. You could use those on the outside of the ring if you prefer and I’ll show you this method on the next channel ring tutorial.
Will you try this method? I find it a bit more time consuming than the resin-only easy method, but the result is a bit more perfect. Please set reasonable expectations for yourself and with your clients though; resin jewellery will never be perfect and that’s the joy of handmade.
I hope you’ve enjoyed this video, please subscribe to my channel and give this video a like to see more like it in the future. Now relax and do some crafting
Please note, this tutorial blog contains affiliate links, meaning I receive a small income based on your purchases from Amazon and Etsy etc. This affiliate income is really helpful to me to support my family and if you’d like to know how I set it all up please see my affiliate page here.
Nikki
*terms apply – some products aren’t included such as settings and findings, sorry.

[…] Slow Speed Ring Turner Tutorial – making bereavement and cremation jewellery using a slow speed ring turner with a direct pour technique. This ring turner is like a slow lathe for filling and getting a perfect result on channel rings. It’s great for UV and epoxy resin and CA glue. This technique is ideal for our channel rings here which are anti-tarnish solid silver. You don’t need a lathe for this tutorial but if you have one, definitely use it for the sanding process. You can see our basic channel ring tutorial here and the advanced channel ring tutorial here. […]